What is a Digital Twin?
A digital twin is a virtual replica of an entity that already exists. Digital twins integrate artificial intelligence, machine learning and software analytics with spatial network graphs to create a digital model. A digital twin integrates historical data and updates itself from multiple sources to represent near real-time status. Often confused with simulations, digital twins differ in that they are used for the entire design-execute-change-decommission lifecycle.
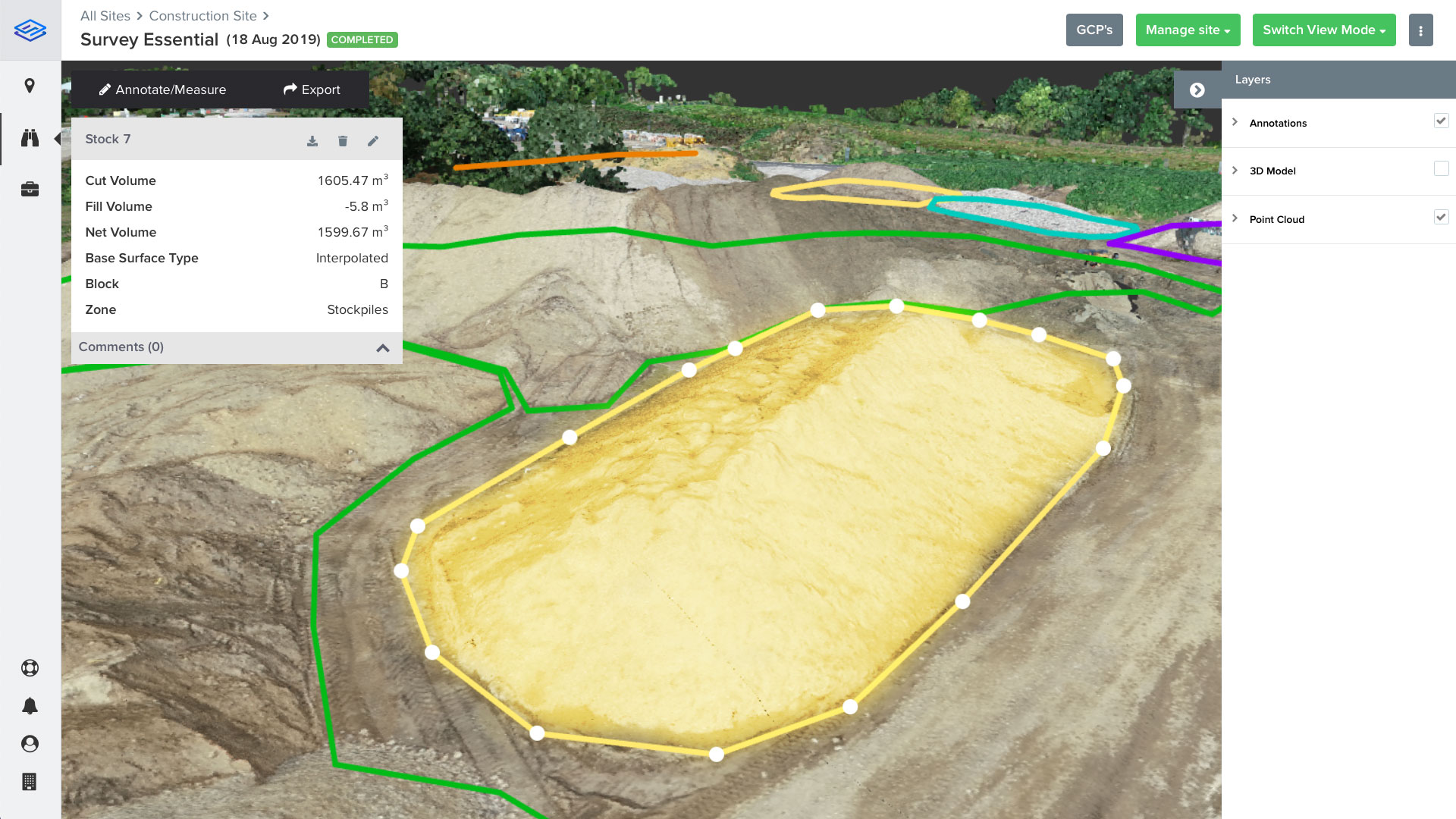
How is a digital twin created?
With a digital twin, you now can review and manipulate your asset digitally without the potential problems involved with changing the physical asset. The level of detail in the Sitemark Fuse platform is what makes it so valuable. We incorporate various different forms of aerial data such as visual and thermal orthomosaics, surface modals, point clouds and 3D models. You can further extend this data with overlays, such as string maps for solar sites. We also generate insights using artificial intelligence, for example with anomalies detected on solar panels, or elements that are built during the construction phase. Additionally, we have more structured data, even to the level of PV panel serial numbers. Connecting all this data delivers many benefits, from enabling predictive maintenance to improving the performance of your site and supporting you in warranty claims if an asset breaks down.
Which industries benefit from using a digital twin?
Construction companies in particular benefit greatly by having a digital twin, the digital representation of a site or project through which all useful information is linked. Digital twins can be used to conduct tests or record events without impacting the built object. The digital twin can be used to visualize how the construction process will evolve, allowing project managers to ensure the success of the project, double check for mistakes and determine what objectives must be met for successful execution. Another benefit is the ability to incorporate raw data and perform digital simulations that are capable of developing blueprints construction companies can follow to maximize accuracy and efficiency.
The safety, practicality, and sustainability of new building designs would also get tested in a digital twin with feedback just as accurate as if the test was executed in real life. For instance, a virtual twin of newly installed scaffolding would monitor every single piece of metal, measure their most important stress points and show developers which locations are under stress. This outcome is capable of saving lives in the real world by utilizing a virtual one.
Mining: Virtual simulations prove to be extremely useful when planning schedules and operations. By simulating the work environment, miners are able to create long-term and short-term schedules and create accurate estimates for drilling, crushing and extraction work and determine what the end product results will be. By simulating the equipment, machinery, and the entire work process, on-site workers are able to test new methodologies on their most crucial work processes in a very cost-effective manner because no capital is required to accurately find out what works – every test will be executed in the digital twin, using the same exact machinery and equipment. The twin enables you to perform stockpile and volumetric measurements, line measurements and grade checks – all safely and accurately.
Solar: While using a digital twin is a staple for those tech-savvy construction and mining companies, it is a relatively new tool for solar stakeholders. If solar site developers would have the ability to test out their ideas in reality-based simulations that would involve all the necessary real-world factors (e.g. panel angle, weather, spacing, etc.), the total timeframe during which they could plan their site and get them approved would be cut exponentially. Think about resolving issues, marking panel replacements, linking in-the-field measurements, correlating thermal inspection data with insights coming from your monitoring systems, all without being on the site in-person or changing a real-world asset. You don’t need to send a human into the field to take measurements, improving overall safety as well as optimizing efficiency. In the future, we plan to integrate even more data into the digital twin, such as data derived from monitoring systems and also allow you to use that data in other applications.
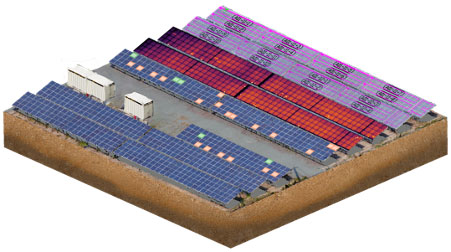
Why Sitemark?
The Sitemark Fuse platform generates a 3D digital twin of your entire solar or construction site, giving you a complete digital replica that can be measured, analyzed and tracked for all your future operational requirements. We also believe in an open system and integrate with other tools through API’s. Giving you a sneak peek regarding an upcoming feature that further helps build the digital twin is BYOD – the ability to bring your own data for input on the Fuse platform. This means you can use data that’s not related to drones; you could upload Lidar point clouds, scanner point clouds and satellite data for example. Keep an eye on our website for upcoming availability!
At Sitemark, our goal is to fuse together the digital and the physical worlds delivering valuable insights. Our vision is to build out the digital twin for the solar, construction and quarrying industries to gather all information in a single place. The possibilities are endless, and we look forward to exploring them with you.