The benefits of drones for thermal solar inspections are well known throughout the industry. They’re beneficial earlier in the lifecycle as well, though.
During the construction phase, drones can offer an efficient way to follow up on the progress and quality of the project.
Here are some best practices you should keep in mind to ensure you get the most out of your inspections, so let’s dive in!
1. Capture a pre-construction scan
The main use-case during the construction phase is progress follow-up, so not many people think about a pre-construction scan. However, it’s beneficial to perform a scan before on-site work happens.
An accurate land survey can help in the design and planning phases of the project. The 3D model of the site generated through such a survey can be used in other tools like PVCase and RatedPower to design your site in a much more optimal way. A drone survey captures millions of points for the elevation model, whereas a manual survey typically only captures hundreds. Besides that, you can easily consider the shading effects of nearby vegetation, trees, or buildings. By including such a level of detail in the planning phase, yield can be increased by 8% while having better visibility of the project’s costs. Overall, that generates a more accurate proposal during the bidding phase, reducing risk and enabling lower margins.
💡 Using an accurate drone survey for plant design can increase yield by 8%.
Additionally, a pre-construction scan offers a lot of value from a warranty point of view. It provides clear proof of the state of the land before work started. For example, a customer was sued once for allegedly destroying a part of a building on a neighboring property. The pre-construction scan clearly showed the building was already damaged before any work started, quickly refuting the claim.
2. Link scan cycles with your use-case
Once entering the construction phase, one of the most common questions is how often you should scan a site. Of course, there’s no golden rule that always works. To determine the flight planning, you should take a moment to consider the use case on which you’d like to focus.
Monthly scan cycles to perform high-level checks of the progress reported by the EPC. The monthly scans create transparency for all stakeholders involved, reduce the risk of counting mistakes, and offer a clear visual track record of the construction for legal cases. The EPC still counts the progress each day or week but creates a stable baseline once every 1 or 2 months.
Weekly scan cycles to implement the progress reporting entirely with drones. Weekly scans streamline the reporting pipeline, eliminate reporting mistakes, and enable regular quality checks. The EPC might still use manual counting for internal planning. Still, regular updates towards the asset owner happen automatically using drone flights. Most companies go for this option.
Daily scan cycles to digitalize the EPC planning process fully. The EPC can focus on optimizing the construction planning, using the automatic progress updates that roll in each day. Daily scans are harder to implement, though, and require proper planning. As drones typically aren’t allowed to fly while people are working on-site, data for the parts on which work happened have to be captured efficiently.
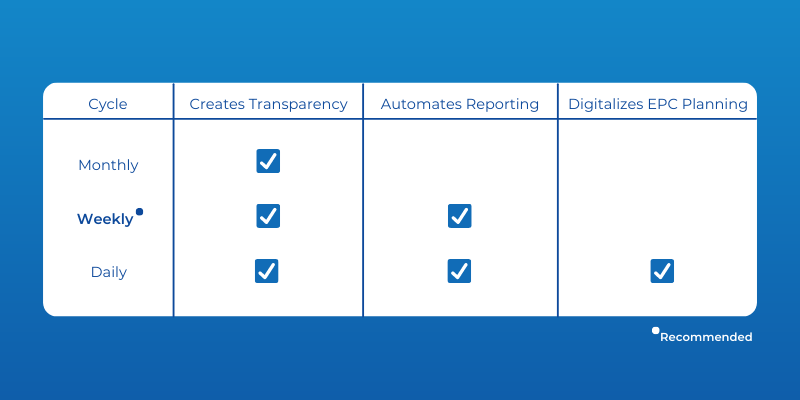
💡 Most customers choose weekly scan cycles to automate the progress reporting between EPC and asset owners.
3. Capture smaller parts of the site
Even though drones are very efficient at capturing data, it doesn’t make much sense to scan parts of the site on which no work happened. Most larger sites are divided into smaller regions for work planning anyway. Suppose additional elements have only been installed on a few of them. In that case, only these have to be scanned again to update the digital twin of the site.
Think about the following types of regions:
- Working regions: at which level will you schedule work on-site?
- Reporting regions: at which levels do you need to report on the progress?
You plan your flight(s) to cover the progressed regions in each reporting cycle. The working regions give you a sense of how much area you have to cover in each reporting cycle. Using the Sitemark Fuse platform, you can easily plan flights to cover one or more regions at once.
We recommend capturing no more than 80Ha in one flight to ensure everything gets processed within 48 hours.
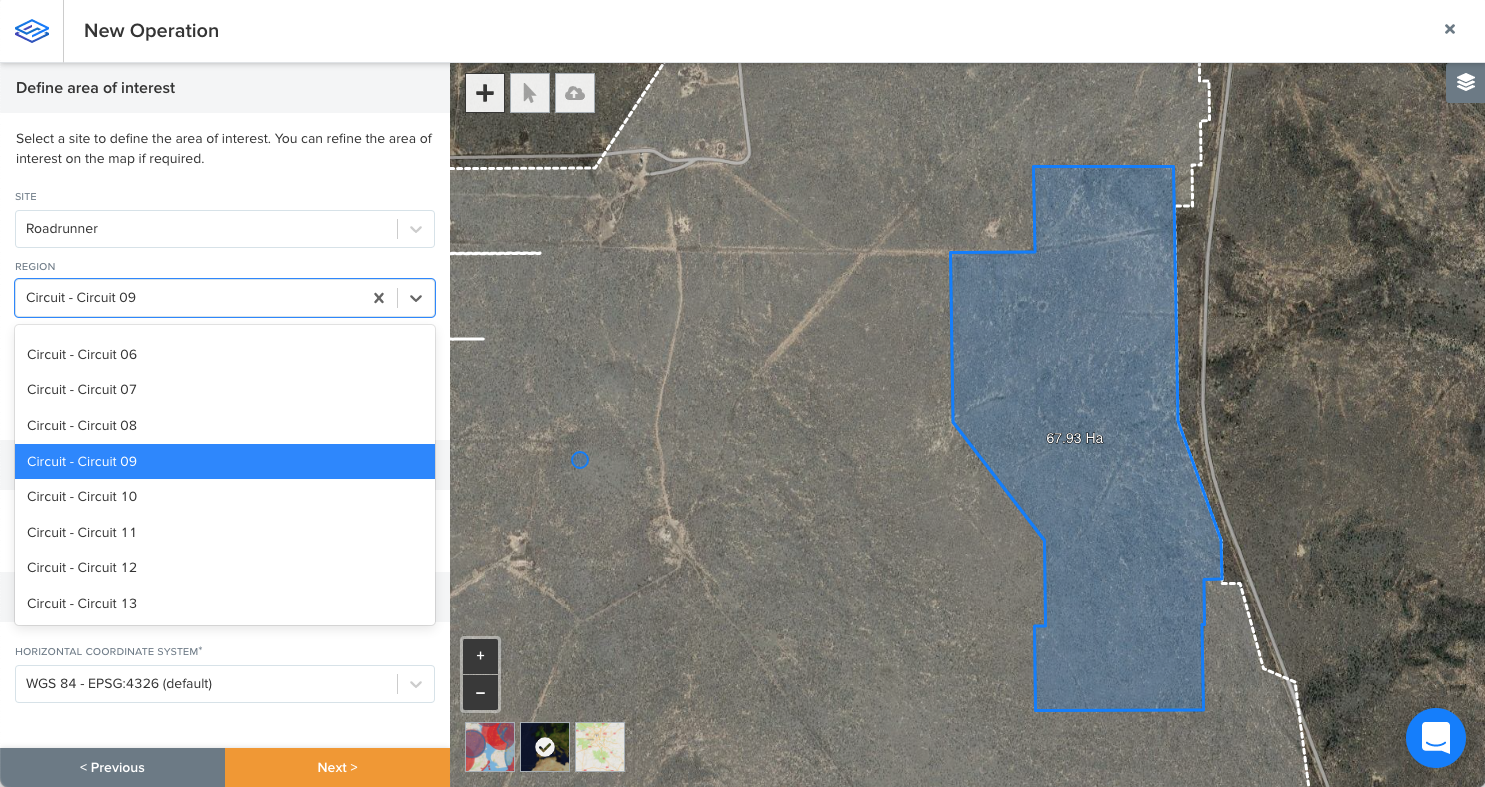
For reporting, different stakeholders require different granularities. A high-level report might contain site-wide statistics, while more granular reports might split the progress by zone. These reporting levels don’t have to be the same as the working regions. Work is typically planned very granularly, while reporting happens at a higher level.
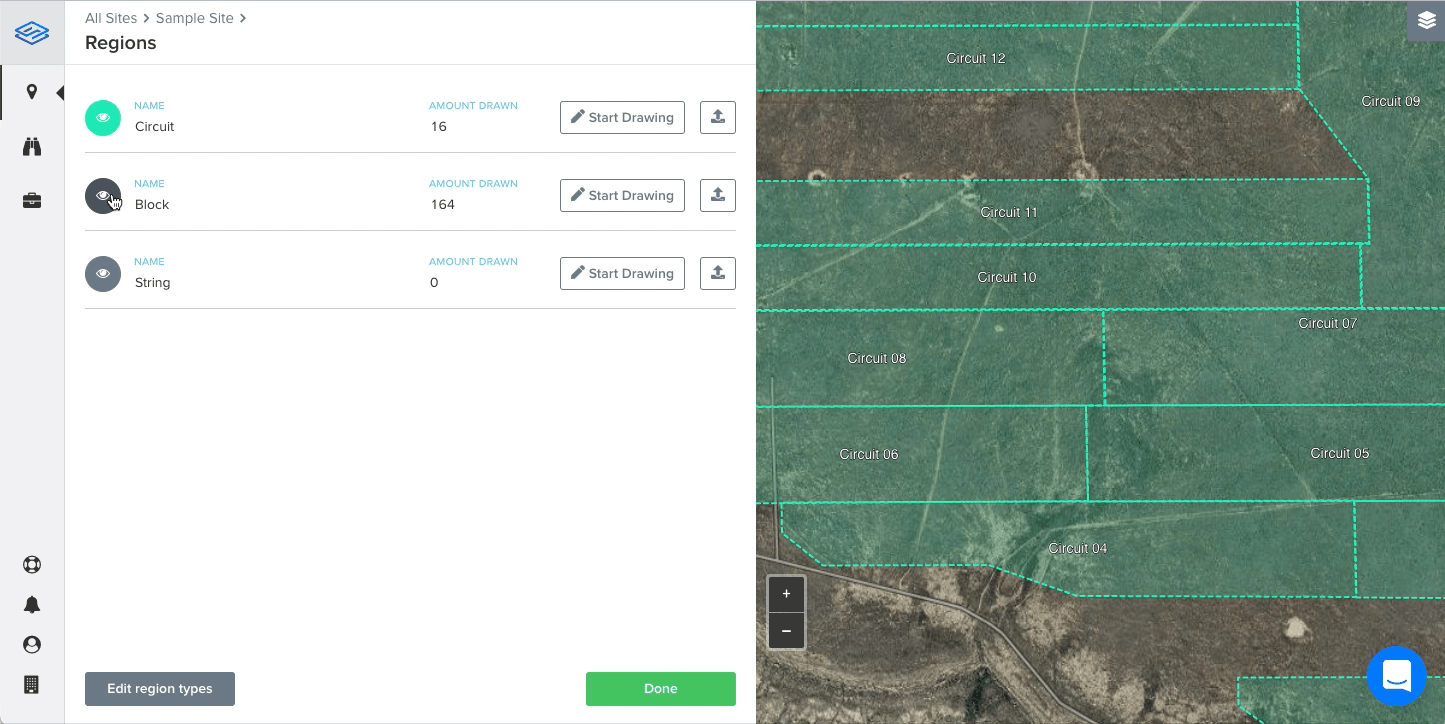
4. Invest in proper site setup
You can capture a lot of interesting information directly by using drones without requiring any additional setup. However, by investing some time in the setup, you can simplify flight planning, streamline reporting, and gain further insights.
First of all, as mentioned above, working with regions has a lot of benefits. Properly defining the different types of regions upfront can significantly simplify the flight planning procedure. You can also reuse these regions for reporting progress on different levels of granularity.
Once you have your regions set up, it makes sense to think about the element targets for each of these regions. How many piles, structures, and modules have to be placed in each? You can transform element counts into completion percentages by adding these targets to the Sitemark Fuse platform.
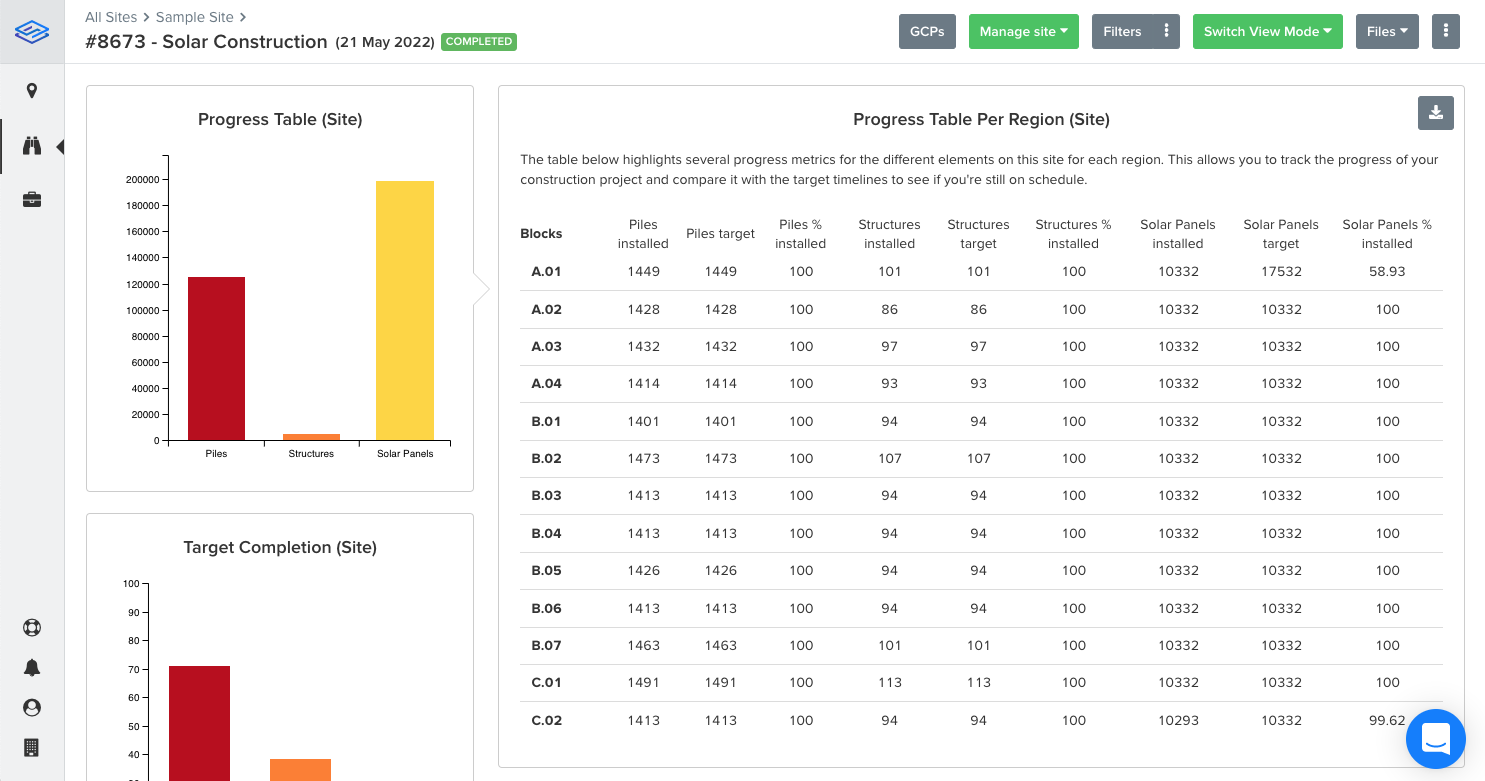
Finally, uploading site designs will enable a rich analysis when the data comes in. You can detect deviations from design, analyze site problems with additional context and allow the Sitemark Fuse platform to report on structures according to your designs.
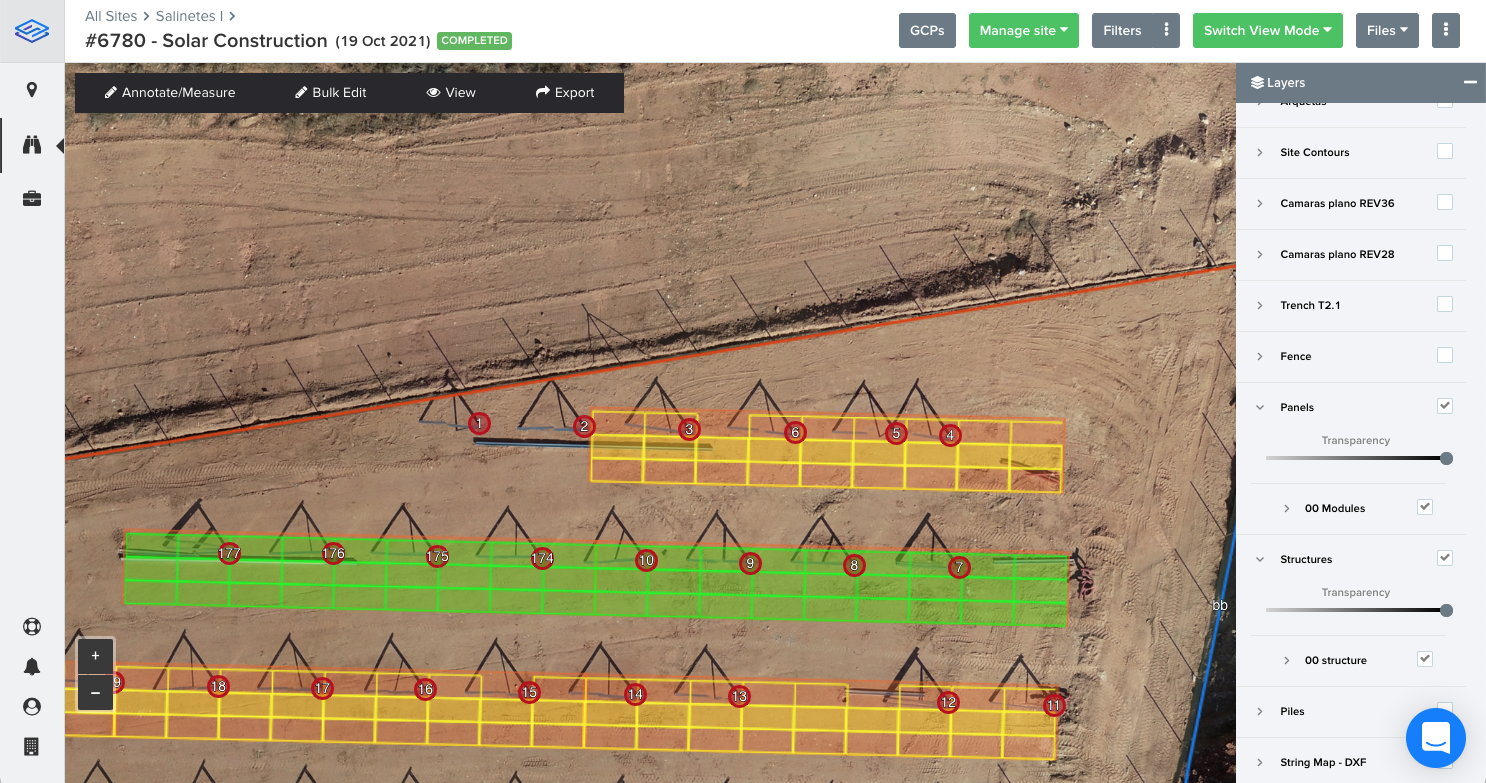
Key take-aways
Let’s take a step back and go over what we’ve learned in this blog post.
First of all, it’s essential to think about what you’d like to use drones for exactly. Do you want to create transparency between asset owners, EPC, and subcontractors, or should they replace all manual counting work for the daily EPC planning? It helps to think about the regions on which you will base your work planning and reporting cycles. Use that information to define the scanning cycle.
Finally, spend some time properly setting up the project in the digital environment to be as efficient as possible when the work starts; you can do that by, e.g., uploading your CAD plans and defining the different types of regions with their construction targets.